Table Of Content

Texture can also provide better product function, such as enhanced grip or reduced wear from friction. Types of textures include matte, gloss, graphics, grains, logos, and geometric patterns. Depending on the type, depth, and location of texture, draft may need to be adjusted to facilitate part ejection, which is determined during the mold design process. For example, the proper grade of steel must be selected so components that run together do not wear out prematurely. Steel hardness must also be determined to maintain the proper balance between wear and toughness. Waterlines must be well-placed to maximize cooling and minimize warping.
Tips for Creating a Healthy and Productive Learning Environment
Molds designs may be as simple as an aluminum prototype MUD insert set to a completed multi-cavity, rotary 2-shot mold with a hot runner and unscrewing mechanism. The timing of the pandemic meant that students, who were completing tooling split designs and starting CNC programming, could not move forward with machining, assembly and molding. Here, we share ideas that we implemented within our teaching to introduce young engineers to the world of injection mold design … virtually. Desktop 3D printing offers businesses a versatile, cost-effective approach to developing master models and molds for both the direct and indirect mold-making processes, entirely in house.
Lighting for Your Home Office: Matching Productivity With Style
The operator then takes the part and manually removes the insert and places it back into the mold for the next part. White paper shares how cooling channel analysis, which collects maximum pressure drop, total flow rate and heat dissipation, eases the performance evaluation of mold temperature controllers. Produce high quality molds at record times; increase your business competitiveness and profitability with the right CAD/CAM solution. Get design guidelines for creating 3D printed patterns, walk through the step-by-step direct investment casting process, and explore guidelines for indirect investment casting and sand casting. Both patterns for indirect mold-making and molds for directly casting metal parts can be made using multiple methods.
Product analysis
The process taken when designing a mold depends on the plastic part to be molded. The process begins with analyzing the plastic part, designing for manufacturing, CAD, mold flow analysis, design confirmation, and mold building. The thickness determines the pressure by which the plastic is injected. If uniformity cannot be achieved, the change should be gradual and not exceed the previous by a large margin.
To execute the project feasibly, we provide a DFM report to review your design and identify any flaws and errors before starting the production process. JB Custom Mold Mfg. accommodates projects of all sizes with the same urgency and commitment to quality. Our clients are assured every run of plastic parts manufactured to very strict tolerance standards. We enjoy a high client retention rate and we do tend to be selective to companies serious about their success and their own quality control. The molding department is capable of molding parts with extremely tight tolerances and dimensional requirements.
Big 3 Precision and Creative Blow Mold Tooling form strategic partnership - PlasticsToday
Big 3 Precision and Creative Blow Mold Tooling form strategic partnership.
Posted: Fri, 01 Dec 2023 06:11:05 GMT [source]
Here, we touched upon all you need to get you started with injection molding. There is plenty more to learn though in our Knowledge Base - a collection of technical articles on all manufacturing technologies, written by experts from Protolabs Network and the manufacturing industry. Use a uniform wall thickness throughout the part (if possible) and avoid thick sections. This is essential as non-uniform walls can lead to warping or the part as the melted material cools down. Add a minimum interference of 0.25 mm between the crush rib and the fitted part. Because of the small surface contact with the mold, crush ribs can be designed without a draft angle.
Basics of Injection Molding Design
In terms of shape, trapezoidal runners are preferred because they are easy to design and use. There are two major techniques for mold making—the direct and indirect mold-making processes. The indirect mold-making approach involves developing molds from a physical master model, or pattern.
Cost reduction tips
Texture can be a functional component of design (for example, to improve grip), as well as a strategy for camouflaging imperfect or frequently handled parts. One way to avoid sink marks is to core out the solid sections of the part to reduce thick areas. If the strength of a solid part is required, try using cross hatched rib patterns inside the cored out area to increase strength and avoid sink. As a rule-of-thumb, make sure that all bosses and locating/support ribs are no more than 60% of the thickness of the nominal wall. Following some basic rules of injection molded part design will result in parts that are easier to manufacture and assemble, and are typically much stronger in service.
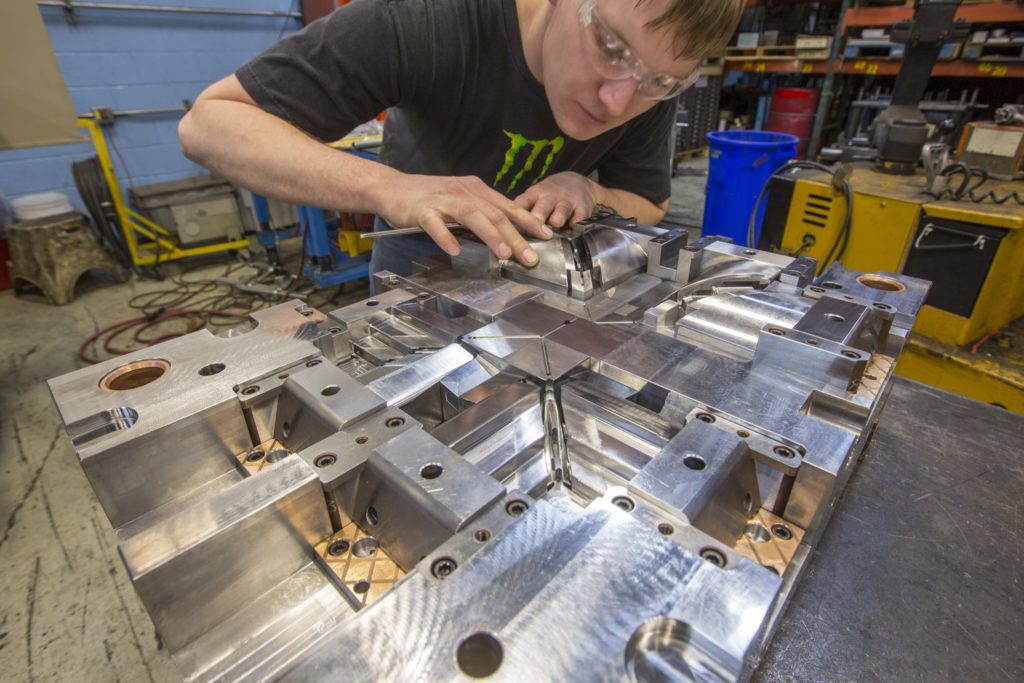
They consist of cylindrical projections with holes designed to receive screws, threaded inserts, or other types of fastening and assembly hardware. A good way to think of a boss is as a rib that closes on itself in a circle.Bosses are used as points of attachment or fastening (in conjuction with self-tapping screws or threaded inserts). Undercuts always add cost, complexity, and maintenance requirements to the mold. A clever redesign can often eliminate undercuts.Shut-offs are a useful trick to deal with undercuts on internal regions of the part (for snap-fits) or on the sides of the part (for holes or handles).
Paloian has an in-depth knowledge of designing parts in numerous processes and materials, including plastics, metals, and composites. Paloian holds more than 40 patents and was past chair of SPE RMD and PD3. He has also written hundreds of design-related articles for many publications. Sub gates are generally used by incorporating a tunnel gate into the side of the part or into an ejector pin (post gate).
A comprehensive process failure mode effects analysis (PFMEA) is also completed. 7.Where the product has plastic surrounding the steel part, it will be difficult to demold. This is caused by the phenomenon of “holding” the steel part due to the shrinkage stress of the plastic melt after cooling. 1.The ejection stroke generally stipulates that the ejected product is 5~10mm away from the mold. For some simple cylindrical products with a large demolding slope, the stroke can be 2/3 of the product depth. Don’t be too long, because the ejector rod is very thin and has a long stroke, which is easy to damage the ejector rod.
Rapid injection molding requires that your part design should be as simple as possible, right? This is another false assumption as we support complex part designs that requires undercuts, through holes and other features. When draft is applied to the outside and inside surfaces in the same mold half, you create a very deep rib that is difficult to manufacture and increases tooling costs. It also increases the chance of mold damage due to difficult ejection and short shots due to lack of mold venting in the deep rib.
How the molten plastic enters, fills, and cools within the cavity to form the part largely drives what form the features in that part must take. Adhering to some basic rules of injection molded part design will result in a part that, in addition to being easier to manufacture and assemble, will typically be much stronger in service. Dividing a part into basic groups will help you to build your part in a logical manner while minimizing molding problems. As a part is developed, always keep in mind how the part is molded and what you can do to minimize stress.
Labor cost can be optimized, however, by working closely with an experienced, efficient tooling team that makes wise decisions on material selection and design tradeoffs, early in the design process. JB Custom Mold Mfg. has served manufacturing businesses in the greater Los Angeles area for more than 25 years. We provide cutting-edge mold design / mold fabrication and thermal plastic injection molding complete manufacturing solutions. For these volumes, the molds are CNC machined from tool steel and can withstand millions of Injection molding cycles.
Hot tip gates are often the most cosmetically appealing gate (about 0.050 in. diameter) and often times can be hidden in a dimple or around a logo or text. The core and cavity are often referenced as the A and B sides or top and bottom halves of a mold. A core-cavity approach to part design can save manufacturing time and money and improve the overall part cosmetics.
They shrink away from the cavity or outer surfaces and around the core or inside of the part. This requires force to eject the part from the core, which is delivered by the ejector pins. Because it requires thinking about where and how the part will be gated. In the Fow Mold industry, we deliver all your injection needs without hesitation and no project is too big for us. We have a team of experienced experts whose work is reputable across China and the world at large. Revamp your product development process with our premium injection molding prototype tooling.
No comments:
Post a Comment